Tack Weld | Types & How Does It Work?
Tack welding is a rapid per-welding method that involves putting small dot-like beads along the length of the joint. The amount of tack welds required is determined by the joint geometry, length, material thickness, and metal type. Tack welding is a key technique that all welders must have in their arsenal. Tack welds are required for almost every welding task, especially for intricate joints.
This article will teach you about tack welding, its purpose, when and how to utilize tack welds, and the many tacks available.
How does Tack Welding Work?
Tack welds are tiny welds spaced evenly along the workpieces. They are typically formed of little beads made of the same material as the final weld. The number of tack welds required is determined by the size of the materials being joined.
Even though tack welds are small and transient, they have nevertheless been considered a sort of welding.
What Is The Use Of a Tack Weld?
Tack welding’s major goal is to keep the workpieces connected so that the final welding may be completed properly.
Furthermore, the tack welds hold the workpiece edges together and preserve the gap.
Tack weld is also used to prevent wedge distortion in some welding processes.
It serves as a rough project outline, allowing faults to be quickly corrected. That is, if the edges are tack welded incorrectly, the welder can remove the racks and recreate the alignment correctly.
Tack welds keep the welding position and orientation stable, preventing overturning or incorrectly attached work components.
Tack welds improve the functionality of welding equipment. Tanks are sometimes utilized in place of fixtures.
Advantages Of Tack Welding
- It provides a cost for creating the final welding to unite two or more work items.
- Tacks can be undone and disabled if they are put in correctly.
- Tacks aid in the strengthening of the joint and the proper maintenance of the joint gap.
- Tacks are used to smooth out and fill gaps even after the final welding.
- Tacks aid in the prevention of joint distortion during welding.
- You can tack weld practically any type of welding material.
Disadvantages Of Tack Welding
- Tacks that are not properly placed can reduce the efficiency of the final welding.
- Tacks may include slag if not well-cleaned.
- Cleaning up after welding is difficult and time-consuming.
- Depending on the metal, you must select the appropriate tack welding procedure.
- Otherwise, it may be ineffective.
- Tack removal can be difficult at times, especially in steel and thinner workpieces.
Tack Welding Challenges
Tack welds must be sufficiently strong to hold the workpieces together. Defective welds can fail when workpieces are moved, twisted, or elevated, causing the joins to pull apart and potentially causing harm to humans and machinery.
Tack welds should not compromise the quality of the finished weld by including faults such as arc strikes, cracks, craters, hard areas, or residual slag and spatter because they are supposed to support the final welding process.
Another issue arises from quenching and cooling the steels usually utilized in the fabrication of pipes and vessels. Quenching and cooling can induce flaws in the base metal if done too quickly. This is because tack welding introduces heat to the workpiece, albeit at a lower level than the final weld. Rapid quenching can result in the formation of brittle and hard, crack-sensitive microstructures in the heat-affected zone. Even after the tack weld is removed by grinding, these faults can still occur near the weld region.
While the final welding process may need a high heat input, tack welds can be formed utilizing technologies such as shielded metal arc welding. This can result in the formation of crack-sensitive and brittle zones, which may not be eradicated even after several high-heat input passes. With the final welding step, this cracking may worsen.
Cracks in the faulty area can form as the weld metal solidifies or when tension is applied to the junction. These cracks may be too small to perceive with the human eye, or they may be hidden behind the weld joint.
Even the slightest crack can grow and eventually lead to a fracture.
The Size And Number of Tack Welds
Tack welds should be tiny enough to easily incorporate into the final weld bead but large enough to securely hold the pieces. It’s difficult to find the appropriate balance between the two. Tack welds, on the other hand, should never be greater than the final weld.
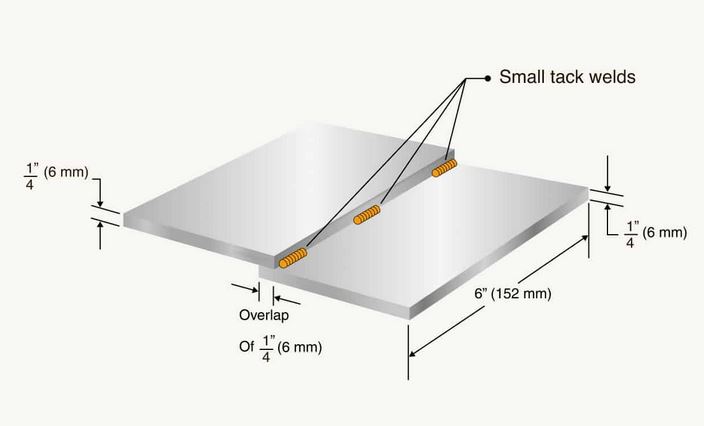
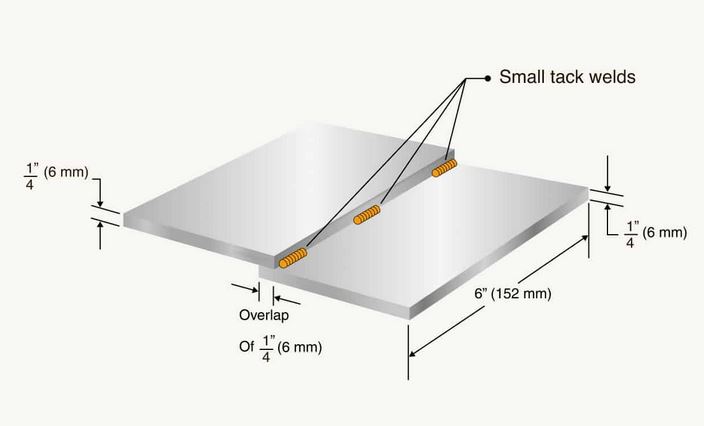
A 1/2-inch wide weld connection, for example, should not include 5/8-inch tack welds.
Oversized tack welds will generate a weld form discontinuity and constitute a substantial stress concentration site.
Consider the following factors when determining the size and quantity of tack welds:
Internal stresses
The more internal stresses the tack welds must withstand while the permanent weld cools, the larger the ultimate weld. As a result, insufficient or undersized tack welds will shatter as the weld cools, even as you proceed along the joint.
Length of the joint
If the joint shape is straight, shorter joints require fewer tack welds. However, if you are welding a curving, short junction, you may need to use several tacks.
Specified tolerance
Depending on the desired joint perfection, you may require more tack welds.
Complex fit up
More tack welds will be required when welding complex joint shapes.
Material thickness
Thin gauges necessitate numerous uniformly spaced small tack welds, whereas large metal pieces can be tack welded in a few places.
How To Tack Weld Metal
Tack welding can be accomplished in a variety of ways.
However, the two most popular approaches are as follows:
Start with the end and then bisect
The tracks are positioned on the ends of the workpiece in this way. Then, moving inside, apply a tack in the center of the joint length. Then switch back and forth. If the material is sensitive and demands high precision, it is preferable to indicate the locations where you want to install tracks.
Move to the ends from the middle
To begin, make marks to locate the joint line’s midpoint. Now, proceed to the ends, alternating on both sides at the desired locations. Put a tack at this precise location.
Types Of Tack Welds
Standard Tack Weld
Standard track welding is a type of tack welding in which the tacos provide support for the final welding.
In this scenario, the tracks provide significant additional support and prevent the joint from breaking.
Bridge Tack Weld
When the welded junction requires a root opening for putting pipes or other things into the gap, bridge tack welding is employed. This method’s major goal is to keep the gaps intact while keeping the work components connected together. It is primarily utilized prior to flux-coated, TIG, and MIG welding.
Small tacks are put to the work parts in this scenario, allowing each side to cool before applying the next tack. Surprisingly, bridge tacks are typically put at a shallow depth rather than deep to the root of the joint.
This is due to the fact that these tacks are deleted after the initial root pass.
Hot Tack Weld
Hot tack welding is used to close gaps that have formed as a result of welding. The welder uses tacks to fix gaps and verify that the welded edge is smooth and not porous or weak.
The welder employs a technique similar to bridge tackling. They used a sledgehammer to bridge the gaps and level the surface after installing the tacks.
Ultrasonic Tack
With small electric or gas welding devices, the welder makes little tacks on the edges’ joints. The machine forces the molten filler materials into the tiny holes created by the workpiece joints at ultrasonic speed.
Why Tack Welding is Important
Tack welding serves numerous uses, including:
- Holding components in place until they may be joined
- ensuring that the components are properly positioned
- Improving the functionality of fixtures or eliminating their use entirely
- Maintaining the appropriate joint gap and preventing workpiece movement
- Assisting in the control of distortion during final welding
- Assuring the mechanical strength of the assembly regardless of whether it is hoisted, moved, or turned
All of these factors contribute to the quality of a final weld, sometimes without the need for fixtures.
Materials that can be Tack Welded
Tack welding may join any material that can be welded by any other joining method. The simplicity with which tack welding can be accomplished, on the other hand, is determined by parameters such as material type and thickness.
Thinner materials may suffer from burn-through or other visually undesirable results, and some materials, such as aluminum, may be difficult to tack weld due to their low melting temperature.
FAQs
When to Tack Weld?
Tack welding is useful when you need to temporarily hold the pieces of a weldment together until the final welds are completed.
This can entail working on the weldment, handling, and shipping.
What is the Tack Weld Symbol?
There is no official tack weld sign, however, the spot weld symbol (a circle) can be used instead to indicate tack welds above, below, or on the reference line.
What does a Tack Weld Hold?
Tack welds are used to hold two metals together temporarily before final welding and can be used in conjunction with or instead of other fasteners.
What is a Bridge Tack Weld?
A bridge tack weld is one that connects two bevels without going through the root. When no longer needed, these can be ground away.
What is an Ideal Tack Weld?
The ideal tack weld fulfills its goal by ensuring proper alignment of the workpieces, preventing metals from warping during welding, and maintaining the required joint spacing. All of this is possible with the proper heat, penetration, and wire flow.
Can You Tack Weld Aluminum?
Tack welding aluminum is possible, however, a filler wire should always be utilized. Tack welding aluminum, like welding aluminum in general, is difficult due to the low melting temperature. However, if you keep a tight arc, utilize a sharp electrode, and guarantee there is no gap while retaining a tiny overlap, it is doable.
Can You Tack Weld Stainless Steel?
Tack welding stainless steel is possible, but it is critical to ensure that the components are put up flush with no gaps between them. Apply a sharp electrode that is less than 1/16″ away from the joint, and use high heat for a rapid burst.
Conclusion
Tack welding is used to hold two pieces of metal together temporarily before a final welding procedure.
These welds ensure that the two workpieces are properly aligned and that the joint gap and orientation are correct.
Tack welds can also reduce metal distortion during the final weld, reinforcing or even replacing fixtures.
This is excellent for low-volume or one-time projects when fixtures may not be cost-effective.
Tack welds, despite being small and easily removed, must be strong enough to accomplish their purpose without damaging the foundation materials.